CNC Lathe Machine Parts: An In-Depth Overview
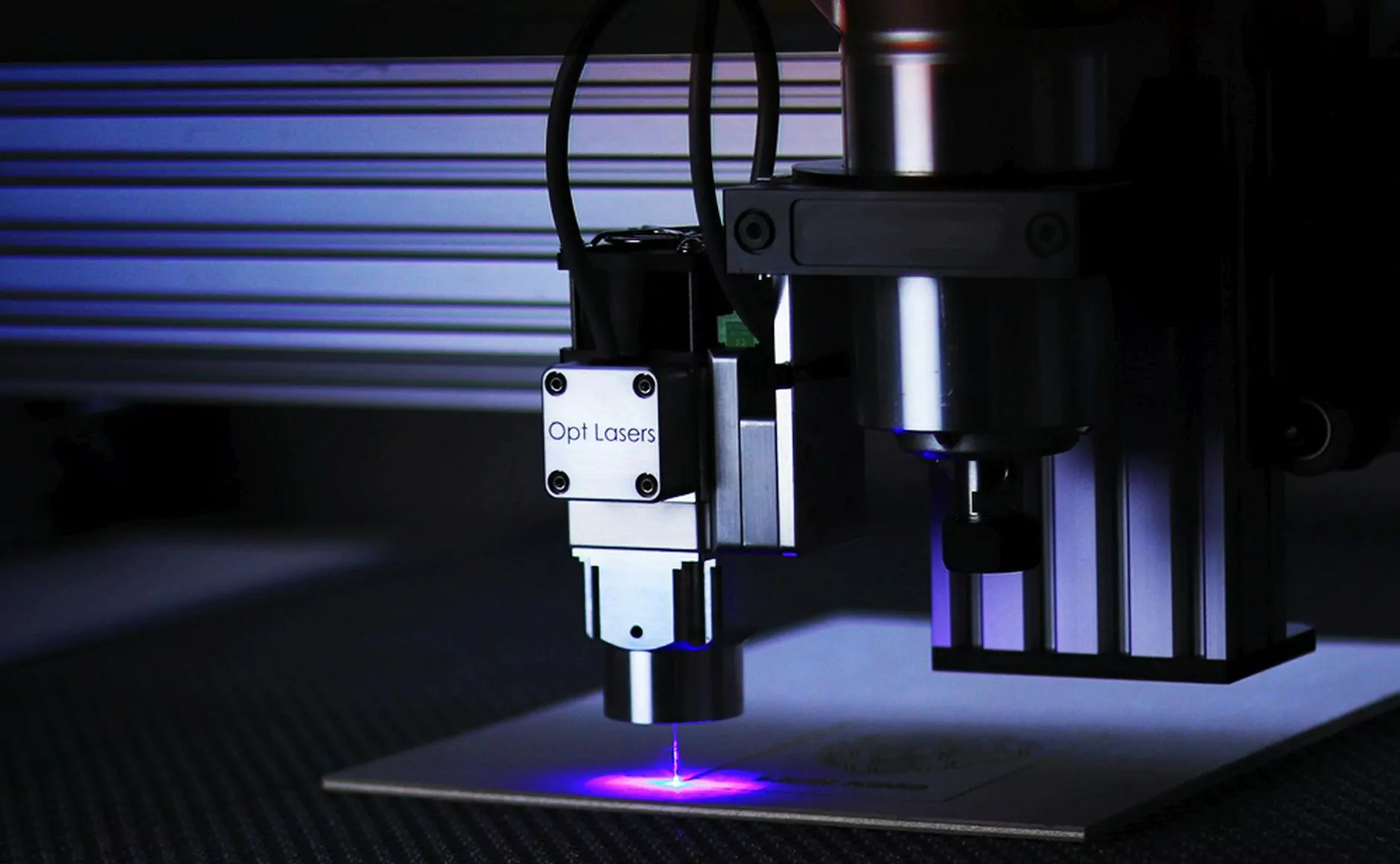
The world of metal fabrication is vast and multifaceted, with numerous processes and technologies that play crucial roles. Among these, CNC machines, particularly cnc lathe machine parts, stand out as essential components, providing precision, efficiency, and flexibility. This article will explore the various aspects of CNC lathe machine parts, their operation, significance, and why they are vital for metal fabricators like Deep Mould.
What is a CNC Lathe?
A CNC lathe is a type of computer numerical control machine that allows for automated cutting, shaping, and machining of materials, primarily metals. A CNC lathe operates by rotating the material against a fixed cutting tool, guided by computer programming, which accurately controls the movement and speed of the operation.
The Functionality of CNC Lathe Machine Parts
To gain a better understanding of how CNC lathes work, it is essential to dissect the key cnc lathe machine parts involved in its operation. Each component plays an integral role in the efficiency and quality of the machining process, contributing to higher productivity rates and enhanced product accuracy.
Components of CNC Lathe Machine Parts
- Main Spindle: It is responsible for holding and rotating the workpiece. The speed and direction of the spindle rotation are crucial for determining the cutting speed and ensuring optimal machining.
- Chuck: The chuck is the clamping device that securely holds the workpiece in place during the machining process. It can have multiple jaws to accommodate different shapes and sizes of materials.
- Tool Post: This component holds the cutting tool and allows for its precise adjustment. The tool post can accommodate various tool types, enabling versatility in machining operations.
- Cross Slide: The cross slide moves the tool post horizontally across the workpiece. It allows for adjustments necessary for turning and shaping the material accurately.
- Bed: The bed is the foundational structure of a CNC lathe, providing stability and support for all other components. Its design and material are crucial for maintaining precision.
- Tailstock: The tailstock supports the workpiece during machining operations, especially for longer pieces. Positioning the tailstock accurately is vital for ensuring that the workpiece remains stable throughout the process.
- CNC Controller: This electronic component serves as the brain of the CNC lathe, interpreting the G-code instructions sent from the computer and controlling the movements of the machine.
The Importance of Quality CNC Lathe Machine Parts
Understanding why the quality of cnc lathe machine parts is paramount can help metal fabricators make informed decisions when investing in equipment. High-quality parts contribute significantly to:
1. Precision Machining
The emphasis on precision is critical in metal fabrication. High-quality CNC lathe parts ensure that each cut and shape is accurate to the specifications required by designers and engineers. This precision is vital in producing components that fit together perfectly and function reliably.
2. Enhanced Productivity
Investing in robust CNC lathe machine parts allows for greater operational efficiency. Quality parts reduce the likelihood of breakdowns and downtime, enabling businesses to meet production targets consistently. Moreover, they often allow for faster cutting speeds without sacrificing quality.
3. Longevity and Durability
Quality components tend to wear less and hold up better under the stresses of continuous operation. Choosing durable CNC lathe machine parts can result in lower replacement and maintenance costs over time, making it a smart investment for metal fabricators.
Choosing the Right CNC Lathe Machine Parts
When selecting CNC lathe machine parts, several factors must be taken into consideration. Here are some useful tips:
1. Assess Your Specific Needs
Understanding the type of materials you are working with and the complexity of the parts you need to produce is vital. Different applications may require different types of machines and parts.
2. Consider the Manufacturer's Reputation
Partnering with established manufacturers known for their quality and service can save you significant time and money. Researching providers or choosing companies like Deep Mould that have a solid reputation in the industry can ensure reliable products that meet your operational needs.
3. Evaluate Compatibility
Ensure that the parts you choose are compatible with your existing equipment. Compatibility can affect not only performance but also safety.
4. Look for Technological Advancements
New technologies can lead to enhanced performance and capabilities in CNC lathe machine parts. Stay informed about the latest advancements and consider integrating modern components that can help streamline your operations.
Maintenance of CNC Lathe Machine Parts
Proper maintenance of cnc lathe machine parts is crucial for extending their lifespan and maintaining machine performance. Here are some practical maintenance tips:
1. Regular Cleanings
Accumulation of dirt and debris can impair the normal functioning of CNC machines. Implement a routine cleaning schedule to keep parts free from contaminants.
2. Lubrication
Ensure that all moving parts are adequately lubricated to minimize friction and wear. Follow the manufacturer's recommendations for lubrication intervals and products.
3. Inspection and Replacement
Regularly inspect the parts for signs of wear and damage. Promptly replacing any worn components can prevent more severe damage to the machine and ensure consistent performance.
Conclusion
Understanding the intricacies of cnc lathe machine parts is essential for both enthusiasts and professionals in the field of metal fabrication. Each part plays a pivotal role in ensuring that the machining processes are efficient, precise, and productive.
Investing in quality CNC lathe components not only increases the productivity and longevity of your machine but also enhances the overall quality of the products being manufactured. Companies like Deep Mould are committed to providing top-notch metal fabrication services, leveraging high-quality CNC technologies to serve their clients effectively.
As the industry evolves, staying informed about the advancements in CNC technology and maintenance practices will empower metal fabricators to lead in this competitive landscape.