China Plastic Mould Manufacturer: Leading the Way in Precision and Innovation
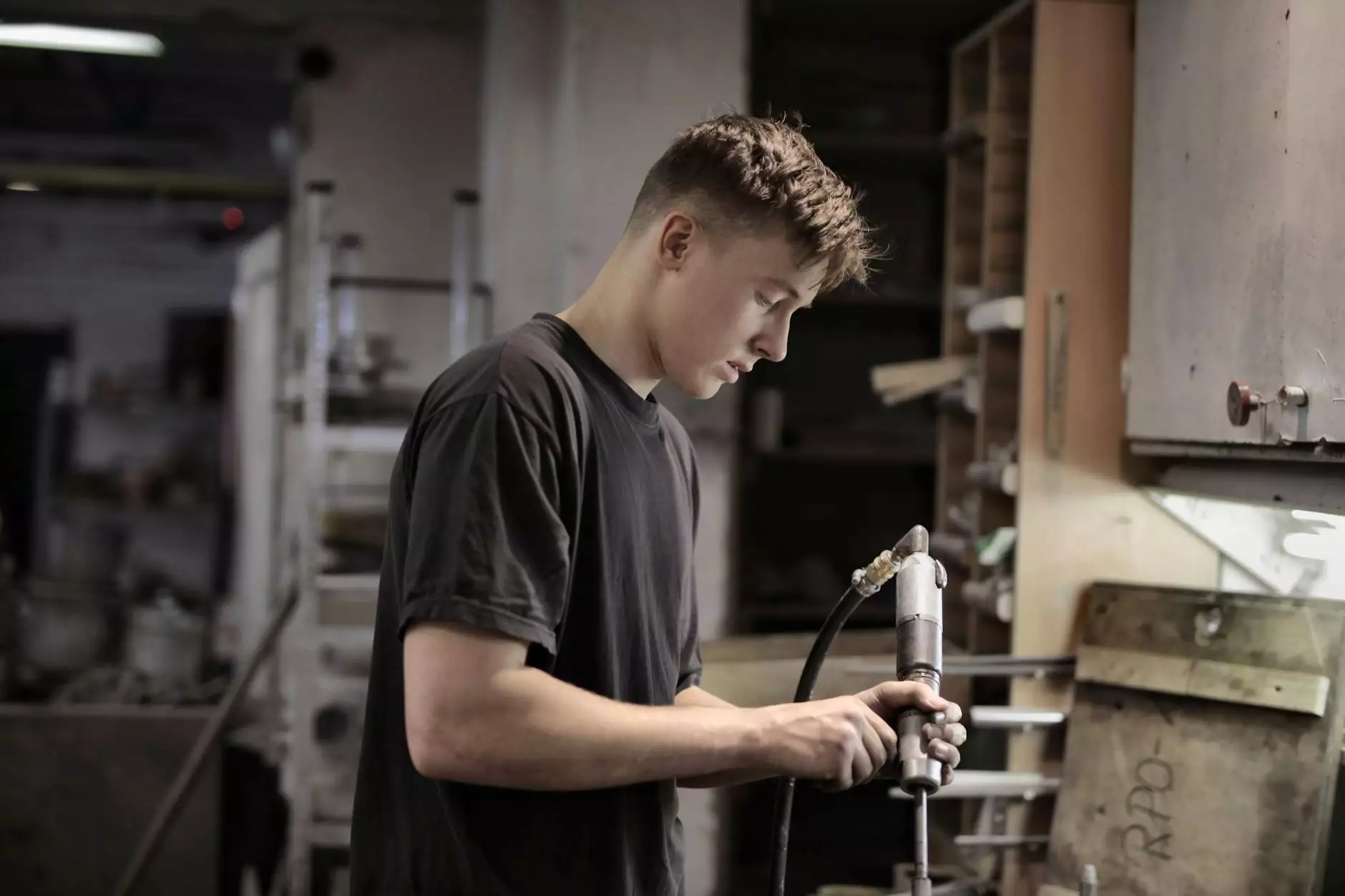
In today's fast-paced manufacturing world, China plastic mould manufacturers play a pivotal role in the global supply chain. The evolution of manufacturing techniques, combined with advanced technology, positions these companies as industry leaders in creating high-quality plastic molds and components. This article explores the significant aspects of the plastic mould manufacturing industry in China, including its processes, technologies, and the benefits it brings to businesses worldwide.
Understanding the Plastic Mould Manufacturing Process
The plastic mould manufacturing process involves several critical stages, each designed to ensure the production of high-quality molds that meet specific client requirements. Here, we break down the key phases of this intricate process:
1. Design and Engineering
The journey begins with the design phase. Engineers use advanced software to design molds that are tailored to the client's specifications. This phase includes:
- 3D Modelling: Using CAD (Computer-Aided Design) software to create detailed models of the molds.
- Simulation: Testing the mold design through simulations to anticipate any potential issues during production.
- Approval Process: Collaborating with clients to finalize designs and ensure they meet all functional requirements.
2. Material Selection
Choosing the right materials is crucial for mold durability and product quality. Common materials used include:
- Steel: Offers high durability and is ideal for high-volume production.
- Aluminum: Lightweight and cost-effective, suitable for low to medium production runs.
- Specialty Alloys: For more specific applications, manufacturers may choose custom materials to enhance performance.
3. Machining and Fabrication
This phase involves the actual creation of the mold components. Advanced CNC (Computer Numerical Control) machines are employed to ensure precision. Key processes include:
- Milling: Shaping the mold using rotating cutters.
- EDM: Electrical discharge machining for detailed features.
- Polishing: Ensuring a smooth finish to reduce defects in the final product.
4. Assembly and Testing
Once the components are fabricated, they are assembled into the final mold. Comprehensive testing is conducted to ensure quality standards are met. This includes:
- Fit Checks: Ensuring all parts fit together seamlessly.
- Test Shots: Running trial production with the molds to check for defects.
- Quality Assurance: Final inspection to guarantee the molds adhere to specifications.
Advantages of Working with a China Plastic Mould Manufacturer
Choosing a China plastic mould manufacturer comes with numerous advantages. Here are some compelling reasons why businesses should consider partnering with them:
1. Cost-Effectiveness
Chinese manufacturers are renowned for their competitive pricing. This cost-effectiveness stems from:
- Lower Labor Costs: Labor expenses in China are typically lower than in many Western countries.
- Economies of Scale: Large production volumes reduce per-unit costs.
- Access to Affordable Materials: Established local suppliers provide materials at reduced rates.
2. Advanced Technology
China's manufacturing sector has embraced advanced technologies that boost efficiency and quality. These include:
- Automation: Robotics in production lines enhance precision and speed.
- Quality Control Technologies: Implementing IoT and AI for real-time monitoring of production quality.
3. Expertise and Experience
With years of experience in the industry, China plastic mould manufacturers have honed their expertise. Their accumulated knowledge leads to:
- Innovative Solutions: Ability to solve complex design challenges.
- Speedy Turnarounds: Efficiency in production without compromising quality.
Applications of Plastic Moulds
Plastic molds manufactured in China find applications across diverse industries. Here are several key sectors:
1. Automotive Industry
In the automotive industry, molds are used to create various components such as:
- Bumpers
- Dashboard panels
- Light housing
2. Consumer Electronics
Plastic parts for consumer electronics require precision and durability. Typical applications include:
- Casings for devices
- Connectors and interfaces
- Internal structural components
3. Medical Devices
The medical sector demands high-quality and sterile plastic components, including:
- Syringes
- Medical trays
- Diagnostic devices
The Future of Plastic Mold Manufacturing in China
As we look forward, the future of plastic mould manufacturing in China appears bright, with several trends shaping the industry landscape:
1. Sustainable Practices
With global awareness around sustainability rising, manufacturers are adopting eco-friendly practices. This includes:
- Using recycled materials in production.
- Implementing energy-efficient processes.
2. Smart Manufacturing
The shift towards smart manufacturing will revolutionize the production process. This involves:
- Integration of AI and machine learning for better decision-making.
- Utilizing big data for optimizing production performance.
3. Growing Export Markets
China's plastic mould manufacturers are expanding their reach into new markets, driven by:
- Increasing demand for affordable, high-quality plastics globally.
- Strategic partnerships with international companies.
Conclusion: Partnering with a China Plastic Mould Manufacturer
In conclusion, collaborating with a China plastic mould manufacturer like Hanking Mould presents an array of benefits that can significantly enhance your manufacturing capabilities. With their cutting-edge technology, cost-effective production, and extensive expertise, Chinese manufacturers are an invaluable asset for businesses looking to innovate and optimize their plastic production. By understanding the intricacies of this industry and leveraging the strengths of your manufacturer, you can ensure that you stay ahead of the competition in a rapidly evolving market.
Embrace the future of plastic molding. Partner with industry-leading manufacturers today and transform your vision into reality!